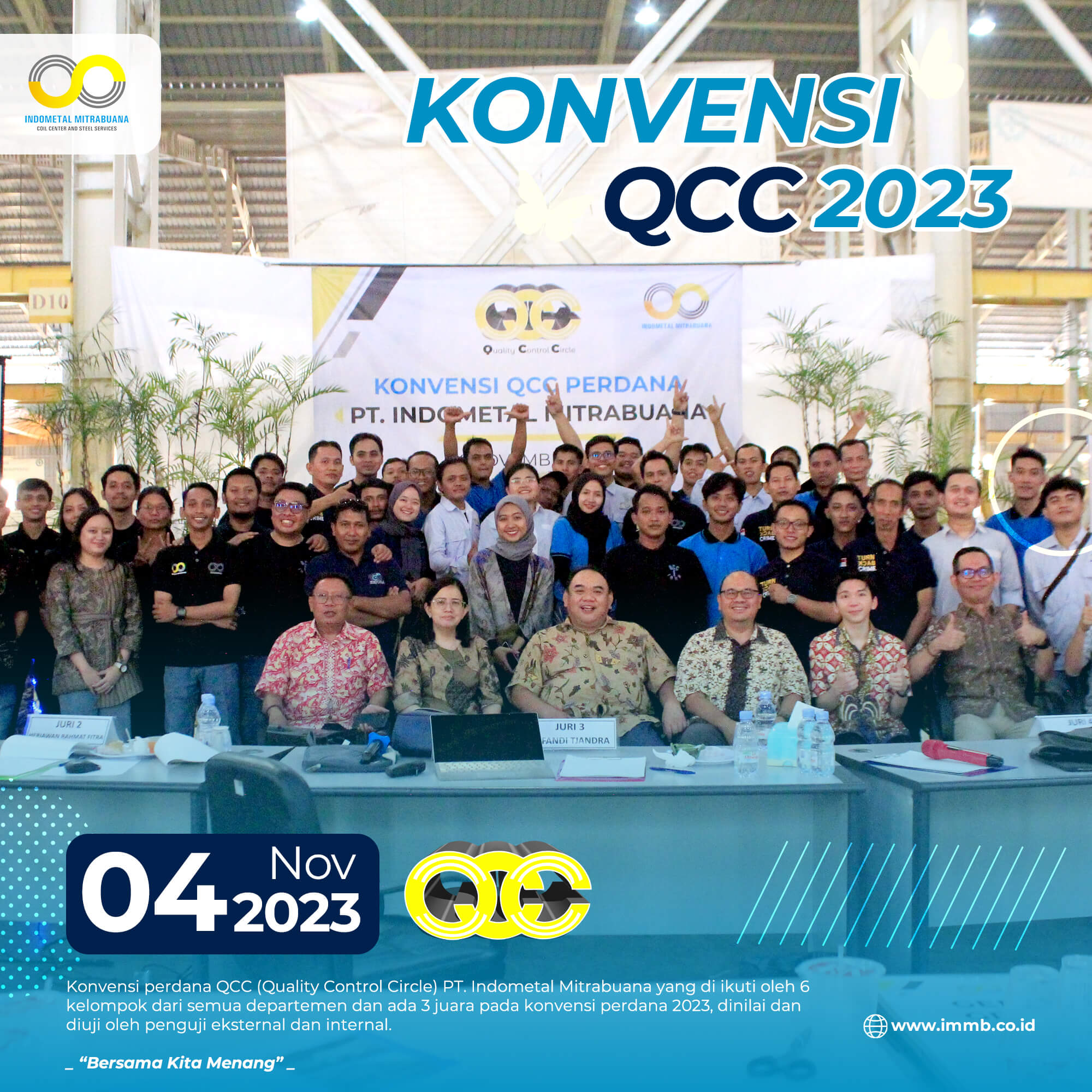
A Quality Control Circle (QCC) is a group of workers, typically from the same work area or department, who meet voluntarily on a regular basis to identify, analyze, and solve quality-related issues in their workplace. The main purpose of a QCC is to improve the quality of products, processes, or services by leveraging the knowledge and expertise of employees who are directly involved in the production or service process.
Key Characteristics of Quality Control Circles:
- Voluntary Participation: Employees volunteer to join QCCs and are typically not forced to participate.
- Small Group Size: The circles usually consist of 5 to 10 members to facilitate effective communication and teamwork.
- Problem-Solving Focus: QCCs focus on identifying problems related to quality, finding the root cause, and proposing solutions.
- Continuous Improvement: The goal is continuous improvement through regular meetings, discussions, and action plans.
- Use of Quality Tools: Members use various quality management tools, such as Pareto charts, cause-and-effect diagrams, flow charts, and brainstorming techniques, to analyze problems and come up with solutions.
- Managerial Support: While the QCCs are self-managed by employees, they often have support from management and may present their findings or solutions to higher-level managers.
- Non-Hierarchical: The group works on an equal footing, with every member contributing ideas regardless of rank or position.
Gallery


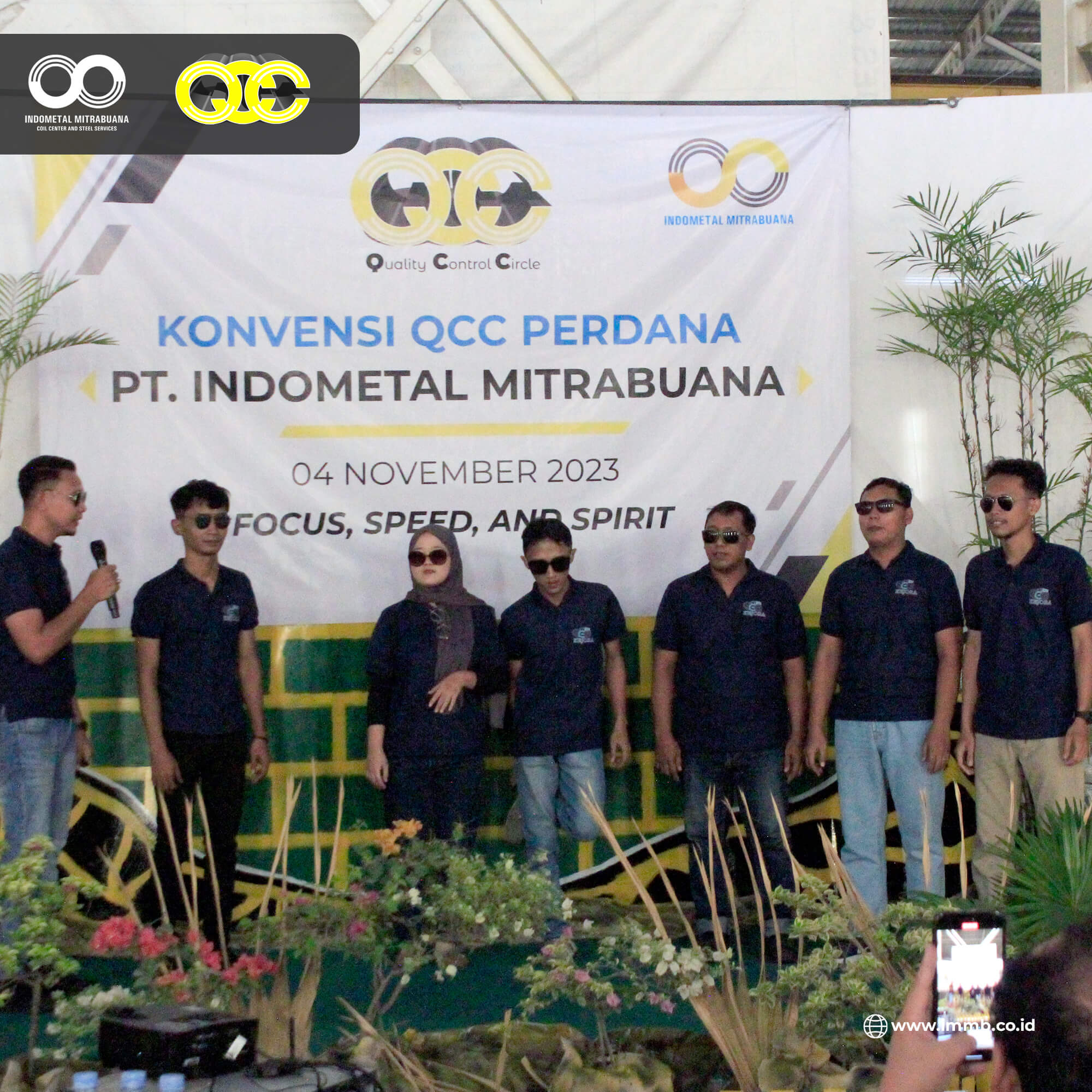
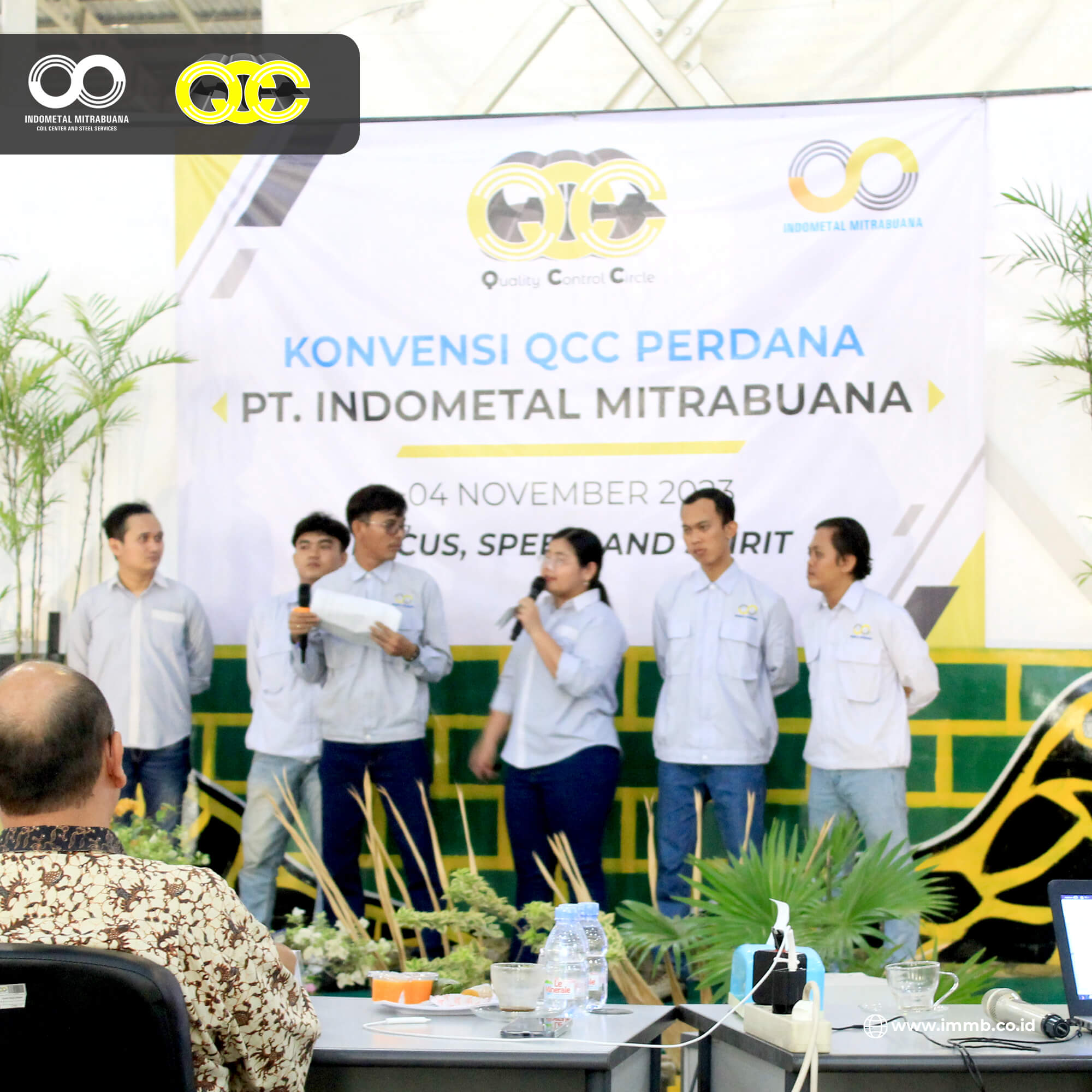
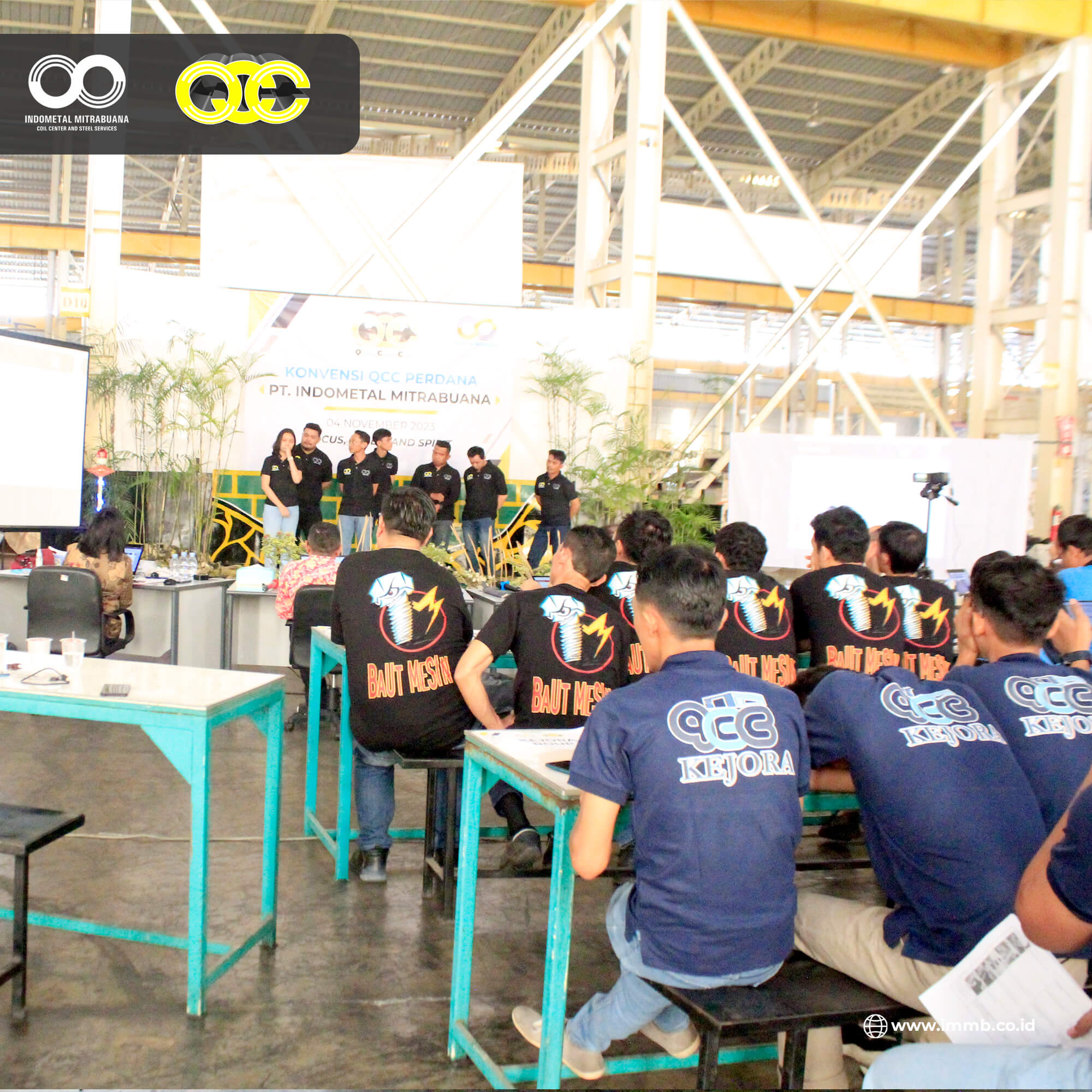


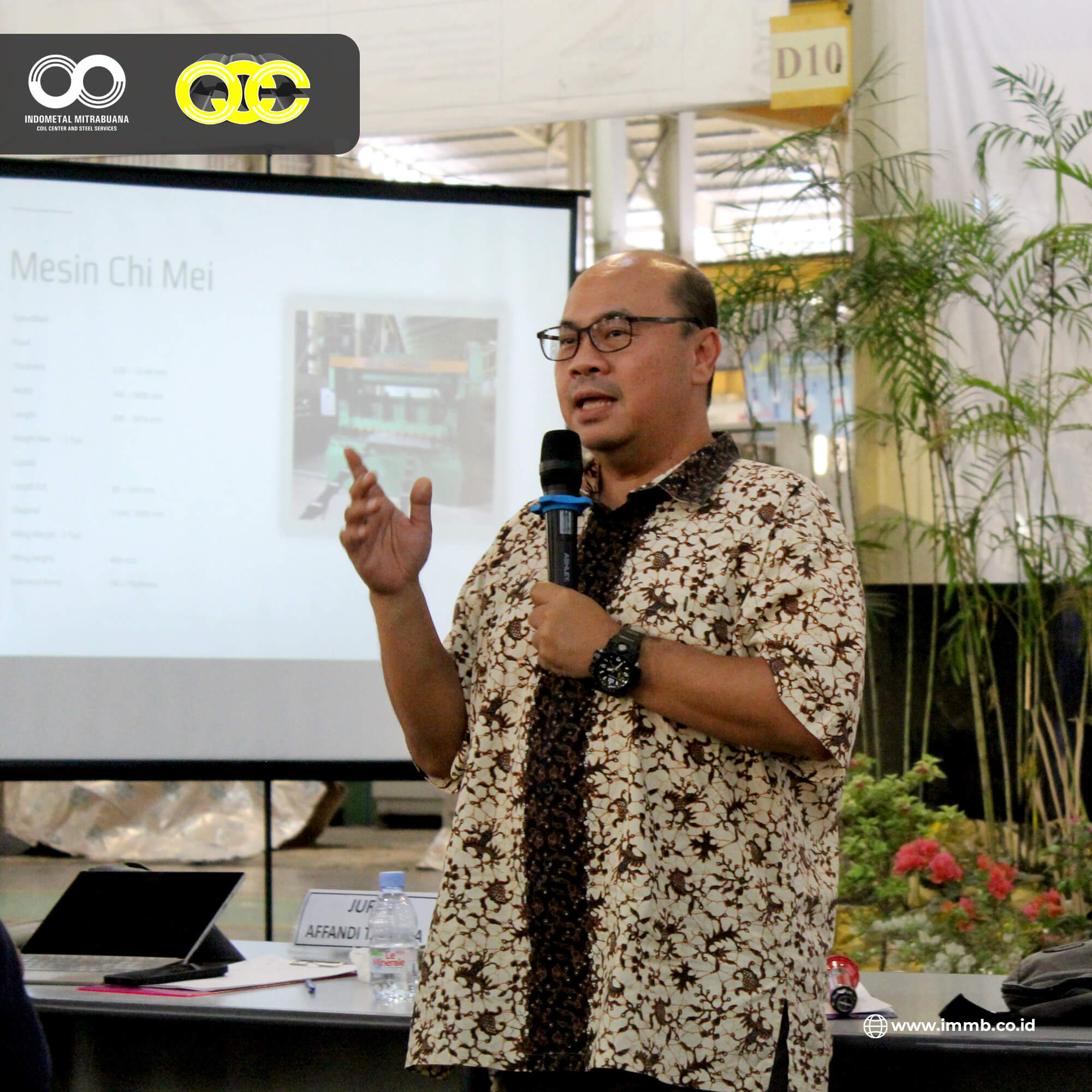
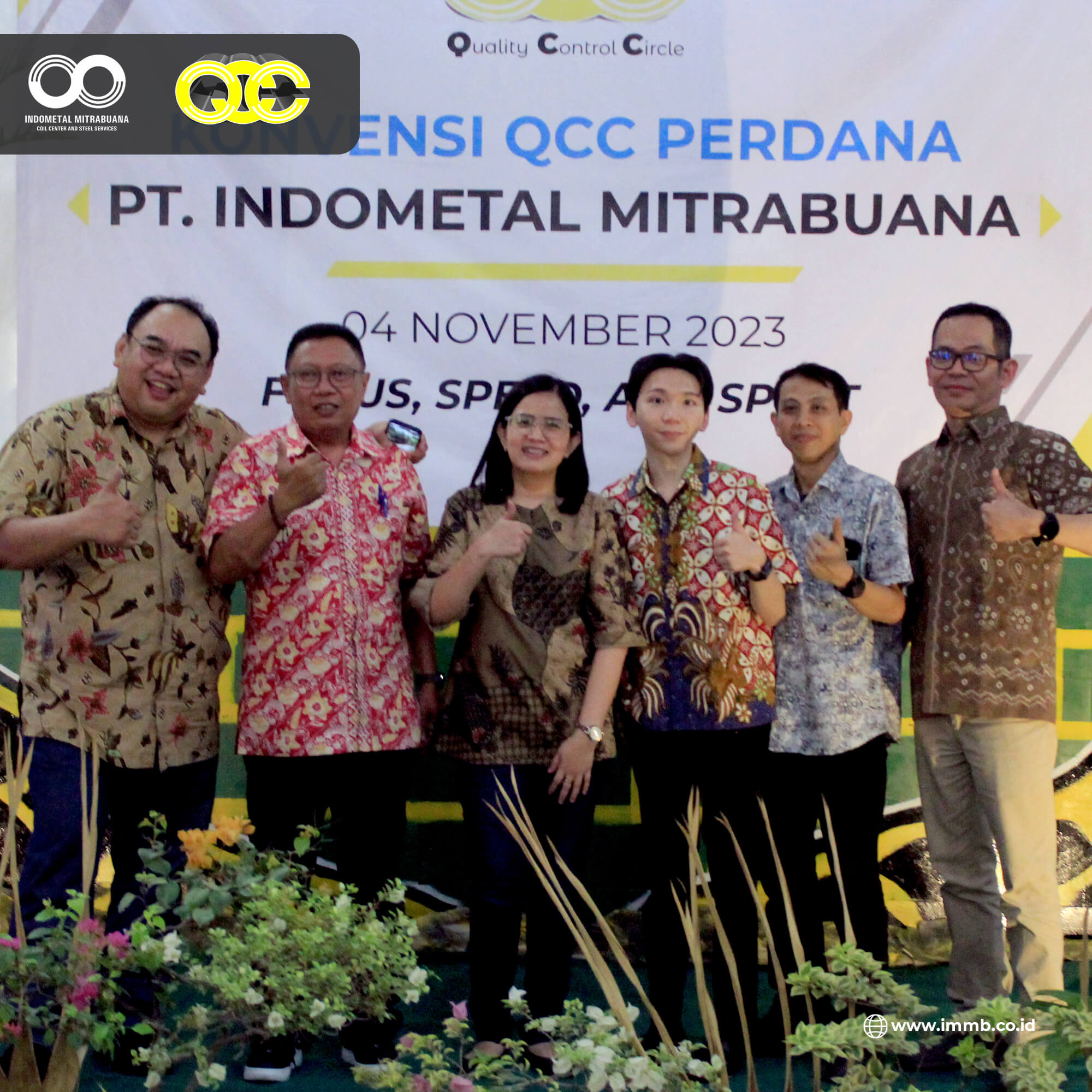
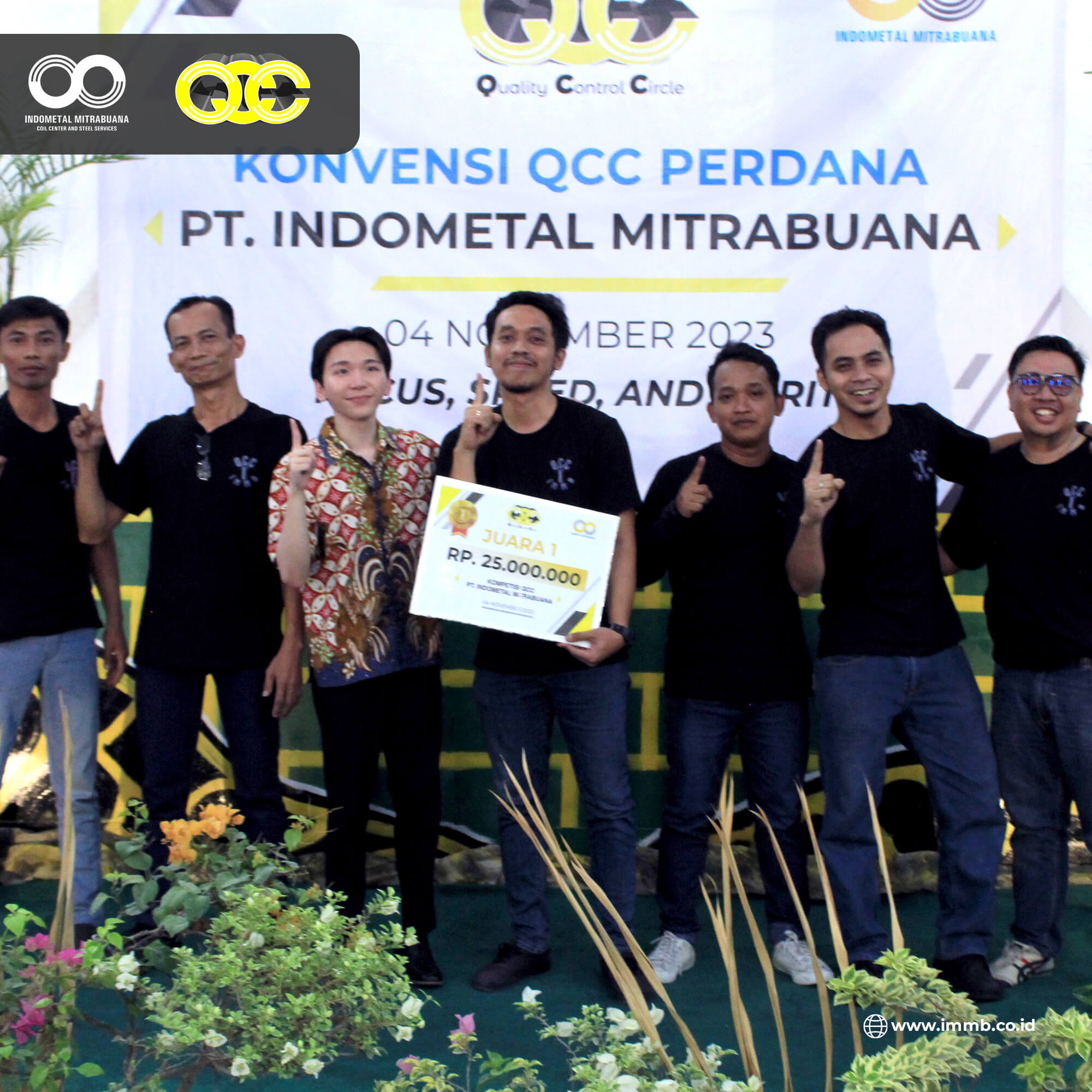


